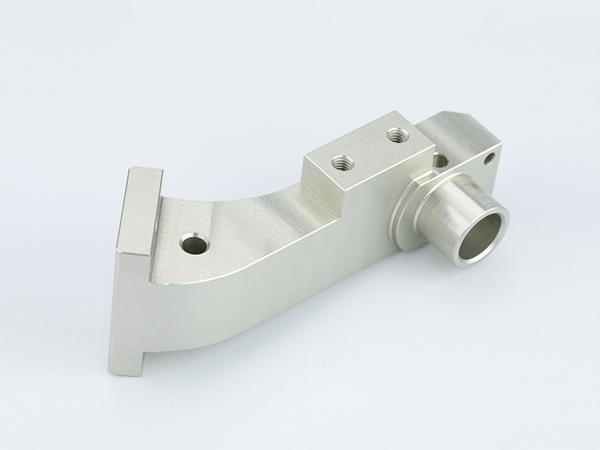
First、 The machining accuracy of metal parts adopts different measurement methods according to different machining accuracy contents and accuracy requirements. Generally speaking, there are the following types of methods:
1. According to whether the measured parameter is directly measured, it can be divided into direct measurement and indirect measurement.
2. It can be divided into absolute measurement and relative measurement according to whether the reading value of the measuring instrument directly represents the value of the measured size.
3. It can be divided into contact measurement and non-contact measurement according to whether the measured surface contacts the measuring head of the measuring instrument.
4. According to the number of parameters measured at a time, it can be divided into single measurement and comprehensive measurement.
5. According to the role of measurement in the processing, it can be divided into active measurement and passive measurement.
6. According to the state of the measured part in the measurement process, it can be divided into static measurement and dynamic measurement.
Second、 Contents related to machining accuracy of metal parts:
1. Dimensional accuracy: refers to the degree of conformity between the actual size of the part after machining and the tolerance zone center of the part size.
2. Shape accuracy: It refers to the degree to which the actual geometric shape of the machined part surface conforms to the ideal geometric shape.
3. Position accuracy: refers to the actual position accuracy difference between the relevant surfaces of the parts after machining.
4. Correlation: In general, when designing machine parts and specifying the machining accuracy of parts, attention should be paid to controlling the shape error within the position tolerance, and the position error should be less than the size tolerance. That is, the shape accuracy of precision parts or important surfaces of parts shall be higher than the position accuracy, and the position accuracy shall be higher than the dimension accuracy.
The machining accuracy of metal parts is mainly used to produce the degree of products. Both machining accuracy and machining error are terms used to evaluate the geometric parameters of machined surfaces. Machining accuracy is measured by tolerance grade. The smaller the grade value is, the higher the accuracy is; The machining error is expressed by numerical value. The larger the numerical value, the greater the error. There are 20 tolerance classes from IT01, IT0, IT1, IT2, IT3 to IT18, of which IT01 represents the highest machining accuracy of the part, and IT18 represents the lowest machining accuracy of the part. Generally, IT7 and IT8 are of medium machining accuracy.
The actual parameters obtained by any processing method will not be absolutely accurate. From the function of the part, as long as the processing error is within the tolerance range required by the part drawing, it is considered that the processing accuracy is guaranteed. The quality of the machine depends on the processing quality of the parts and the assembly quality of the machine. The processing quality of the parts includes the processing accuracy and surface quality of the parts. Machining accuracy refers to the degree to which the actual geometric parameters (size, shape and position) of a part after machining conform to the ideal geometric parameters. The difference between them is called machining error. The machining error reflects the machining accuracy. The greater the error, the lower the machining accuracy, and the smaller the error, the higher the machining accuracy.
Asset metal is a 100% high-tech company from ID to solution, focusing on the application manufacturing of metal parts such as CNC machining, metal stamping and chemical etching.