· Beryllium copper
· Brass
· Cold rolled steel
· Copper
· Nickel
· Plastic
· Phosphor bronze
· Stainless steel
· Copper telluride
· Nickel silver
· Iron
The most common electroplating surface treatments are
· Gold plating
· Silver plating
· Chemical nickel plating
· Platinum, palladium, rhodium plating
· Copper plating
· Electroplating Nickel plating
· Alloy plating
· Chrome plating
· Zinc plating
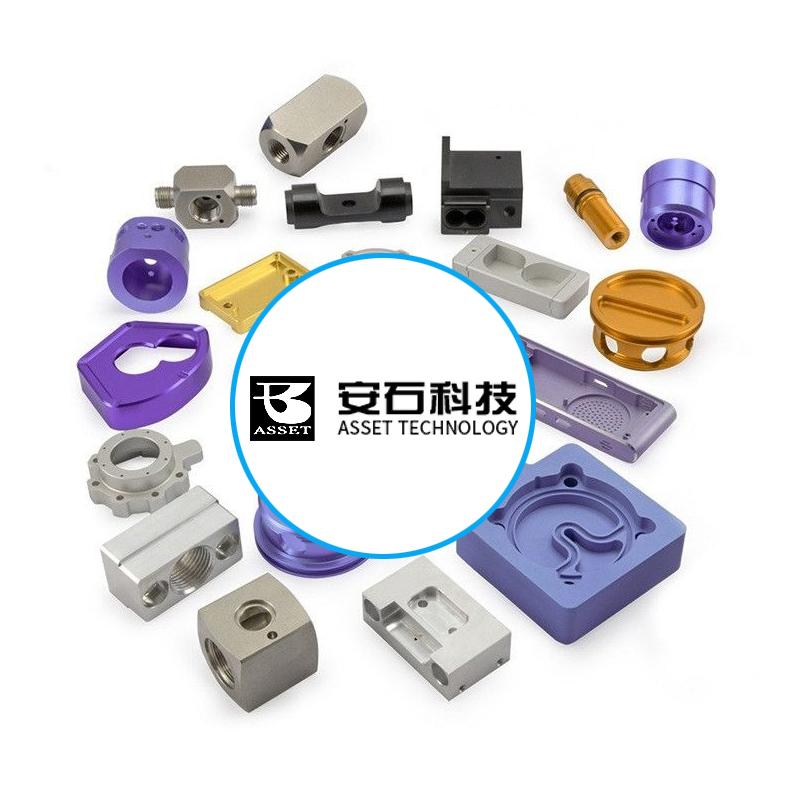
Plating materials, plating methods and plating parts will vary according to the application.
Electroplating provides excellent electrical conductivity, making it one of the best choices for electrodes, conductive pins and PCB circuit board components. Gold is ideal for application in a wide range of environmental and climatic conditions to protect against intense heat and corrosion.
Because of its low resistance, silver plating is also often used in electronic components (copper silver plating process).
Nickel plating is the most common, because it has excellent chemical corrosion resistance, at the same time has higher wear resistance, nickel plating greatly increases the life cycle of the product. Nickel could replace silver in electrons, or it could be used as a surface layer for steel instead of products made from more expensive stainless steel. Nickel also provides a bright surface finish and can be adjusted to half light, full light, sand surface, etc., according to customer requirements.
Copper plating is usually used as an intermediate coating before depositing the final metal layer. This surface finish is most commonly used in circuit boards, automotive parts or the defense industry. Adding copper to the part before the final metal is deposited also improves the overall beauty of the finished product.
It is also possible to co-deposit two or more metals for plating alloy deposits if a single metal does not provide the desired properties. An example is the copper/tin/zinc alloy, also known as Tri-Metal or Tri-M3, provided by specialty electroplating companies.
Asset metal has been focusing on electroplating processing for more than 15 years. We always adhere to the quality and development, the quality and the integrity of the market, and with domestic and foreign sophisticated processing equipment, high-precision testing equipment, with high-quality R & D team, and continue to process high-quality products. We are willing to work with you hand in hand to create a win-win situation.